The Scientific Research Behind Porosity: A Comprehensive Guide for Welders and Fabricators
Understanding the intricate devices behind porosity in welding is vital for welders and producers striving for impressive workmanship. From the composition of the base products to the ins and outs of the welding process itself, a plethora of variables conspire to either worsen or minimize the presence of porosity.
Recognizing Porosity in Welding
FIRST SENTENCE:
Assessment of porosity in welding reveals vital insights into the honesty and quality of the weld joint. Porosity, identified by the presence of tooth cavities or gaps within the weld metal, is a typical problem in welding processes. These spaces, otherwise correctly attended to, can endanger the structural stability and mechanical properties of the weld, causing possible failures in the completed item.

To spot and measure porosity, non-destructive screening techniques such as ultrasonic screening or X-ray examination are usually employed. These techniques permit the identification of internal problems without jeopardizing the integrity of the weld. By evaluating the size, shape, and distribution of porosity within a weld, welders can make informed decisions to improve their welding processes and attain sounder weld joints.

Variables Affecting Porosity Development
The occurrence of porosity in welding is influenced by a myriad of aspects, ranging from gas protecting effectiveness to the ins and outs of welding parameter setups. Welding criteria, including voltage, existing, travel speed, and electrode kind, also effect porosity formation. The welding method used, such as gas metal arc welding (GMAW) or protected steel arc welding (SMAW), can influence porosity formation due to variants in heat distribution and gas insurance coverage - What is Porosity.
Impacts of Porosity on Weld Top Quality
The existence of porosity likewise weakens the weld's resistance to corrosion, as the entraped air or gases within the gaps can react with the surrounding atmosphere, leading to degradation over time. In addition, porosity can prevent the weld's capability to endure pressure or influence, additional endangering the overall top quality and dependability of the bonded framework. In vital applications such as aerospace, automobile, or structural building and constructions, where security and resilience are paramount, the destructive impacts of porosity on weld quality can have extreme consequences, stressing the value of reducing porosity via appropriate welding techniques and treatments.
Techniques to Lessen Porosity
To enhance the top quality of welded joints and make certain structural honesty, welders and producers use particular strategies targeted at lowering the formation of gaps and cavities within the product during the welding process. One reliable method to decrease porosity is to guarantee correct material preparation. This consists special info of comprehensive cleansing of the base steel to remove any type of contaminants such as oil, grease, or dampness that could contribute to porosity development. Additionally, utilizing the ideal welding parameters, such as the appropriate voltage, existing, and travel speed, is vital in preventing porosity. Preserving a regular arc size and angle during welding likewise helps in reducing the likelihood of porosity.

Making use of the ideal welding method, such as back-stepping or employing a weaving movement, can also assist distribute warmth uniformly have a peek at this site and lower the possibilities of porosity formation. By carrying out these techniques, welders can effectively lessen porosity and produce high-quality welded joints.
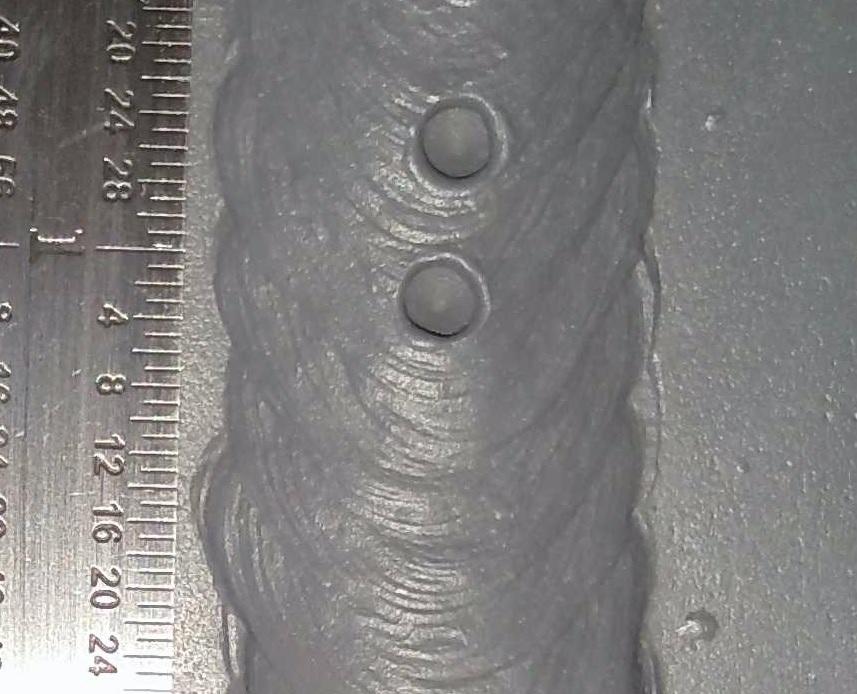
Advanced Solutions for Porosity Control
Applying cutting-edge innovations and ingenious approaches plays a critical duty in attaining superior control over porosity in welding processes. In addition, employing sophisticated welding strategies such as pulsed MIG welding or changed atmosphere welding can likewise aid mitigate porosity problems.
One more sophisticated option entails the Look At This use of innovative welding tools. As an example, utilizing devices with integrated attributes like waveform control and advanced source of power can boost weld quality and reduce porosity threats. The application of automated welding systems with precise control over parameters can significantly minimize porosity defects.
Additionally, integrating advanced monitoring and evaluation technologies such as real-time X-ray imaging or automated ultrasonic testing can assist in detecting porosity early in the welding procedure, permitting instant corrective actions. On the whole, incorporating these sophisticated services can significantly improve porosity control and boost the total high quality of welded parts.
Final Thought
In final thought, recognizing the science behind porosity in welding is essential for welders and producers to produce top notch welds - What is Porosity. Advanced solutions for porosity control can better enhance the welding procedure and ensure a strong and reliable weld.
Comments on “Expert Advice on What is Porosity in Welding and How to Resolve It”